In addition to maintaining central control of daily maintenance information, the control center is continuously evolving to offer rapid support no matter what, even in major disasters. Even if telephone lines are cut, JES has developed a web-based disaster receiver, called Web Entry System (WES), to allow direct communication with elevator passengers and response to rescue and repair requests through a QR code. The pursuit of increased safety never ends.
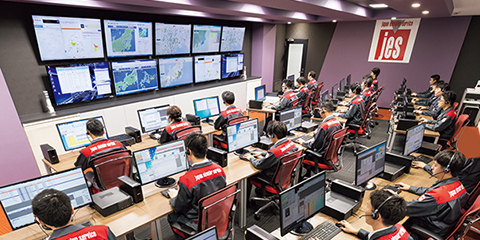
The Control Center uses GPS terminals to monitor the current locations of technical personnel in real time in order to quickly rescue and restore operations in the event of an emergency situation such as a lock-in. In addition to their locations, we have also established a system that allows us to know the experience and means of transportation of each technical personnel and dispatch the most appropriate one to the site immediately. In the event of a large-scale disaster, we quickly set up a task force and activate the disaster system in accordance with the JES disaster manual. It serves as a command post for the early recovery of managed properties and controls each office, branch office, and technical personnel.
PRIME Remote Inspection Service
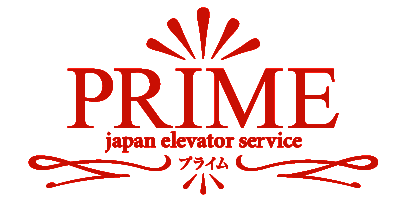
Always monitors the condition of the elevators for a immediate action in the event of an malfunction.
GPS Network
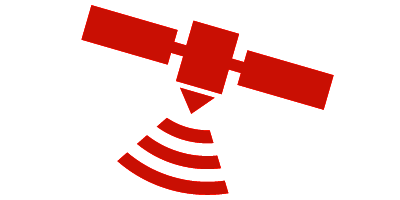
Manage the position of technical personnel using GPS devices in real time, and dispatch the most appropriate one to the site.
Telephone Line Network
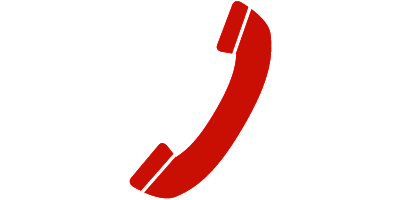
Our staff is always on standby to check and respond to the situation by talking directly to the user in the elevator.
The JES Group led its competitors in introducing a remote inspection service to monitor elevator operation status and condition from a central location. This service, developed using multiple patented technologies, detects faults at the earliest moment, enables response before they occur, and shortens inspection downtime. Also, when faults do occur, it diagnoses causes before staff arrive, enabling smoother recovery.
01 Maintenance on behalf of personnel 24 hours a day, 365 days a year
Benefits
Reduce elevator downtime due to fewer manned inspections
02 Thoroughly grasp elevator operation status and condition
Benefits
Respond before problems occur, reduce breakdown rates
03 Detects small abnormalities, like issues in door action or floor alignment, which can lead to bigger trouble
Benefits
Allows smooth recovery because technical personnel know the situation before they arrive on-site